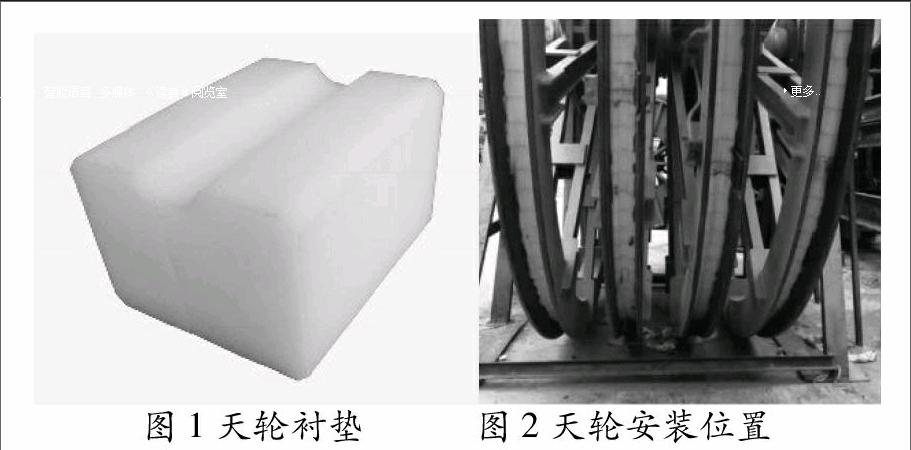

摘要:
在对天轮衬垫使用特性及材料特性分析的基础上,进行深入的切削工艺选择研究,通过对比分析得出车铣加工工艺更优的结论。制定了基于车铣复合加工技术,并以实现高精度加工为目标的详细加工工艺路线。经过实际车铣加工实验,实现了天轮衬垫的高精度加工。质量检测结果表明:车铣复合加工对天轮衬垫的加工完全达到了设计要求,并在质量及加工过程的把握上完全优于传统的车削加工工艺。
关键词:天轮衬垫;车铣复合;工艺分析
引言
天轮是矿井提升系统中主提升钢丝绳导向的重要部件。在长期运行中,天轮衬垫上的绳槽会产生磨损。更换新绳后,新绳由于与旧绳槽不吻合而产生剧烈磨损,寿命急剧降低,极大的增加了投入成本。因此在每次更换钢丝绳时,必须对天轮绳槽进行切削修整,使钢丝绳与绳槽相吻合而提高其使用寿命。现行天轮衬垫的切削采用车削加工工艺,普遍存在着车削精度低,底径一致性差的问题,并容易存在啃刀、震刀等缺点。本文结合现代车铣复合加工工艺的特点,对天轮衬垫的加工工艺进行改良,得出较为优异的天轮衬垫加工工艺。
1 传统加工方法中,加工天轮绳槽的工艺缺陷
在切削加工领域,应用最多的是车削和铣削加工。目前,市场上的绳槽切削装置都是采用车削方式,且车槽装置都是针对主提升机,尚没有很好的针对天轮工况的车槽装置。多绳摩擦式提升机车槽装置过去基本都采用单刀进给、分次手动车削的方式。这种车槽方式对于切削天轮绳槽存在着不足之处:传统车床上的加工工件质量较小,主轴转速快,加工平稳,加工精度较高。但天轮一般直径在3米以上,质量较大,惯量大,转动速度也慢了许多。对其进行车削时,由于天轮磨损半径偏差相对较大,加工表面质量差等,容易存在啃刀、震刀、切削精度低等缺点。且由于车削工艺的加工特性及天轮的基本特性无法改变,因而很难找到有效的解决办法。
随着矿井开采深度、煤矿产量及提升量的增加,天轮衬垫的磨损愈发剧烈,对天轮衬垫的切削质量要求越来越高,传统的车削工艺已不能满足需求。在此背景下,车铣复合加工工艺以其诸多优越性可被运用在天轮衬垫绳槽的加工。
2 车铣复合加工天轮绳槽的工艺优越性
车铣复合加工技术是二十世纪八十年代初发展起来的一种机械加工方法,它不是单纯的将车削和铣削两种加工手段合并到一台机床上,而是利用铣刀旋转和工件旋转的合成运动完成工件表面加工,使工件在形状精度、位置精度、表面粗糙度及残余应力等多方面达到较高要求的一种先进切削加工方法。车铣加工包括铣刀旋转、工件旋转、铣刀轴向进给和径向进给四个基本运动。铣刀的旋转运动是主切削运动,切削速度由铣刀旋转速度和工件旋转速度共同决定。依据工件旋转轴线与刀具旋转轴线相对位置的不同,车铣复合加工可以分为轴向车铣、正交车铣和一般车铣。其中轴向车铣和正交车铣是应用最为广泛的两类车铣加工方法,轴向车铣的铣刀轴线和工件的旋转轴线平行,它不但可以加工外圆表面,也可以加工内孔表面。正交车铣的铣刀轴线与工件的旋转轴线垂直,它不能加工内孔,但在加工外圆表面时铣刀的纵向行程不受限制,可以采用较大的纵向进给,因此在加工外圆表面时,加工效率较高,也是目前应用最为广泛的加工方式。在本文中,也是采用正交车铣的方法。
相比传统车削加工,该加工工艺在加工时具有进给量较小、进给速度慢、铣削速度快等特点,有效地解决了老式切削设备切削绳槽时存在的啃刀、震刀、切削精度低等问题。且车铣复合加工更容易排屑,热变形较小,几乎不会产生由于离心力导致的工件变形。同時工件的超低转速可以消除因工件偏心而产生的振动,使得切削过程更加平稳。由于切削力小,使机床和刀具承受的负荷也变小,利于保证机床的刚度,进而提高了机床的精度,加工平稳。同时,采用车铣复合加工降低了天轮绳槽表面的弹性变形量,提高了加工表面精度及整体几何精度。
3 车铣加工天轮衬垫工艺分析设计
如图1和图2所示,天轮衬垫是天轮上保护天轮绳槽磨损的重要部件,承担着钢丝绳的载货重量及各种动载荷、冲击载荷等。在长期的天轮运行中,衬垫上的绳槽会逐渐磨损。当磨损量超过天轮安全平稳运转所需要满足的要求后,必须对天轮衬垫上的绳槽进行切削修整。由于天轮衬垫是安装在天轮外缘的衬垫槽内并起摩擦拉动钢丝绳的作用,所以天轮衬垫具有一定的耐腐蚀性及耐磨性等,常用的天轮衬垫材料有尼龙、塑料、聚氨酯等[1-2]。
图1天轮衬垫图2天轮安装位置
(1)车铣类型选择
当今,车铣加工大致可分为两大流派:欧式风格和日式风格。日式车铣复合加工是以高速度、小切深及大进给为基础来确定机床参数的,利用了刀具的上限切削速度,适合于模具圆角和材料较软的被加工零件切削。欧式车铣复合加工是以重切削为条件,即大切深、大进给及高线速度来确定机床参数的[3]。结合天轮衬垫的材质相对较软,所费成本较高及天轮对衬垫加工的高效要求特性,选择日式车铣复合加工,即高速度、小切深为基础来确定机床参数较为适合。同时由于每次天轮的切削进给总量较小,因此无需进行大进给加工而采用小进给加工,以进一步减小衬垫的切后弹性变形量,提高衬垫的表面加工质量。
目前,天轮衬垫的加工主要采用传统的车削工艺加工,且车铣复合技术主要应用于大型和常规零件的加工,在这里我们将这一技术与天轮衬垫的绳槽表面加工相结合,拓展了车铣技术的应用领域,同时丰富了天轮的加工工艺方式。
(2)车铣加工阶段的划分
加工工序的划分与加工路线的确定是加工的重要环节。它关系着加工工件的加工质量、加工刀具的磨损情况以及机床的合理使用等。一套完全的加工工序中,要体现“粗加工→半精加工→精加工”的顺序[4]。在本次加工工序中,采用粗车铣刀进行粗加工,实现天轮绳槽的大幅度修正,以降低精加工刀具的磨损,待粗加工完成后,进行半精加工,直至精加工。同时,利用半精加工与精加工的换刀时间间隔,使半精加工后零件的变形得到充分恢复,以提高零件的加工精度。endprint
(3)加工路线的确定应考虑零件加工后变形最小的原则
这是加工小型高质量要求零件的必须注意事项。除了必要的车铣加工阶段的划分外,一般采用逐次减小切深和进给量,提高切削速度的方式实现加工天轮衬垫的小应变变形。同时,配合分多次走刀加工,实现天轮衬垫的小变形恢复部分的切除,达到零件的最终尺寸。精加工时采用日式车铣的高转速、小切深以及小进刀量实现衬垫表面绳槽的高精度加工。
(4)切削用量选择
车铣加工凸轮切削用量通常包括进给速度、切削速度和切削深度等。进给速度的参数标准要根据工件精度、表面粗糙度、材料性质以及刀具等要求共同确定,并且进给速度在粗精加工将近完成时应适当放缓。其原则主要包括:基于质量保证的高进给速度,通常为10~15mm/min;適当减缓进给速度以确保加工精度与表面粗糙度,通常为5~10mm/min;当刀具回原点或空行程时,则选择最大进给速度即可[5]。切削深度的选择与机床、工件、刀具的刚度紧密相关,刚度允许情况下,尽量使切削深度等于工件加工余量,这样能够减少走刀次数,提高生产率。切削用量的选择是多样灵活的,需要根据工件加工的实际情况和要求来确定适当的切削用量。本论文中车铣刀主要使用的是圆角立铣刀,其刀片材料为硬质合金:铣刀的直径为D=40mm,铣刀齿数值Z=2刀具的使用费用为一个2000元。进刀速度为粗加工2mm/min,当
图3车铣复合加工天轮实验
粗加工的加工余量接近4mm时改为半精加工,
进刀速度为1mm/min直至加工至2mm余量。换为精加工车铣刀头,精加工速度为0.5mm/min,当精加工余量接近结束时,再逐次减小切深和进给量,提高切削速度。配合分多次走刀加工,实现天轮衬垫的小变形恢复部分的切除,达到零件的最终尺寸。经试验结果证明:绳槽的车铣加工过程平稳,绳槽表面加工变形量小,加工精度高,最高可达到0.1mm完全满足天轮的加工要求,如图3所示。
4 结论
(1)车铣复合加工避免了传统车削加工中的啃刀、震刀、车削精度低等缺点,提高了加工效率,同时也保证了加工的高精度及可靠性等。
(2)车铣复合加工技术是加工天轮衬垫的有效方法。由于采用铣削电机的高转速运动,在天轮衬垫的绳槽修正上更具特色。通过特制半弧形刀具,完成了绳槽几何外形的高精度修整。同时,依靠天轮的低速转动,实现天轮绳槽表面高质量的完整加工。
[参考文献]
[1]杨帆,孟国营,吴炳胜. 多绳摩擦提升机天轮衬垫的有限元分析[J]. 煤炭工程,2011,(03):99-101.
[2]邓宇翔,彭永朝. 多绳摩擦提升机天轮衬垫材料的改进[J]. 起重运输机械,2015,(12):124-125.
[3]王华侨,张颖,钟志胜. 数控车铣复合加工中心典型设备选型对比应用(下)[J]. 金属加工(冷加工),2012,(23):34-36.
[4]刘克非,刘海生,李春平,张之敬. 微小型座体零件的车铣加工技术[J]. 机械工程师,2007,(07):16-18.
[5]陈艳芬. 车铣加工凸轮轴工艺优化设计研究[J]. 科技与企业,2015,(05):188.
(作者单位:1.安徽理工大学机械工程学院,安徽 淮南 232001;2.淮南矿业集团,安徽 淮南 232001)endprint
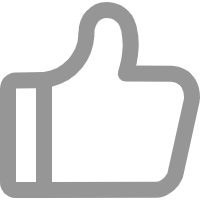
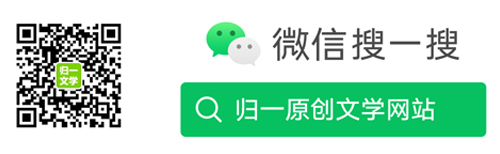