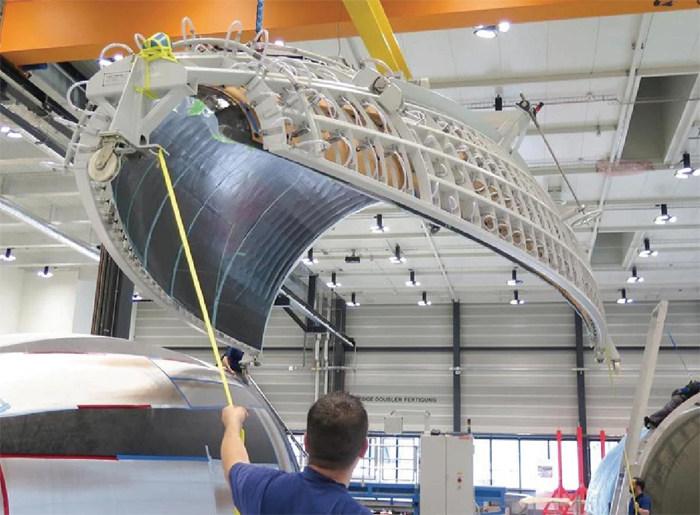
在追求先进性和经济性的过程中,越来越多的复合材料在各类民机主承力或次承力结构上得到应用,然而復合材料高昂的制造成本成为其进一步扩大应用的重要阻碍。
针对复合材料的成本控制,国内外提出了复合材料低成本制造工艺,大多为非热压罐成型工艺,包括液体成型(LCM)工艺等。但液体成型工艺由于技术成熟度等原因,在民机领域的应用还需开展进一步的研究和验证工作。因此,全球航空制造业迫切需要对于现有热压罐成型工艺进行改进,研究如何降低复合材料制造成本,实现复合材料性能与成本的平衡。
制造成本分析与控制
美国军民用飞机制造商及其主承包商早期提供的信息表明:在利用热压罐技术成型的复合材料产品成本组成中,材料占15%,铺层占25%,装配占45%,固化占10%,紧固件占5%。由此可见,零件制造成本占总成本的比例是很大的。
复合材料制造成本通常可分为材料成本、工时成本和工装成本,其中材料成本和工时成本为重复成本(Recurring Cost,RC),工装成本为非重复成本(Non-recurring Cost,NRC)。
复合材料的材料成本包含预浸料、蜂窝等主材的采购,以及制造过程中要用到的工艺辅料和胶漆等化工材料、材料运输和管理成本等,其中主材成本占比较大,主材成本由材料采购单价和实际用量决定。
工时成本为制造中所耗费的工时费,由耗费时长和小时费率决定,包含设备工时和人工工时,工时可按制造工序拆分,工序由工艺方案决定,如领料、工装准备、铺层、打袋、固化、机加和测量检测等,其中铺层和固化工序的工时成本通常占比较大。
工装成本为制造过程中的工装夹具费用,通常指为提高生产速率而配备增加的工装,但不包括研制阶段的工装,研制阶段的工装属于研制成本。
虽然制造成本在生产阶段才发生,但产品成本的60%-70%却是由设计过程决定的。因此,在设计阶段考虑成本因素,对于降低复合材料产品的制造成本具有显著的作用。在设计阶段,应从构型选择、铺层设计、工艺方案和生产模式等方面考虑,识别材料利用率、铺贴和固化等成本关键参数,降低材料成本和工时成本,达到制造成本控制。
面向制造成本的结构设计
影响飞机成本的决定因素是设计思想、设计水平和设计工程师在设计过程中的成本意识,在设计阶段考虑成本因素,对于降低复合材料产品的制造成本具有显著的作用。
面向制造成本的结构设计,通常从结构形式、材料选择和公差设定等方面考虑。在结构形式方面,在满足结构强度、刚度和工艺性的前提下,尽量选择简单的结构形式,减轻结构重量,降低复合材料结构的工艺制造难度。结构设计同时考虑可制造性,尽量选择可用成熟稳定工艺制造的结构方案,缩短制造工时,保障制造合格率,控制制造成本。
在材料选择方面,根据复材结构承力设计特征,合理选择材料体系,要选择采购较容易且使用比较普遍的材料,尽量以国内稳定供货渠道为主,同时尽可能减少材料种类,便于后续材料批产采购。
在公差设计方面,综合考虑重量、强度、疲劳强度、损伤容限要求,考虑放大公差的裕度设计,确定合理的产品缺陷接收限,提高产品制造合格率,保证制造的经济性。通过复合材料产品制造验收技术条件控制,给出合理的制造缺陷接收限。
提高材料利用率,降低材料成本
在材料成本中,主材成本占比通常大于70%,其总价值为材料采购单价乘实际用量,而实际用量则取决于理论用量和材料利用率。因此,降低材料成本有两种思路,一是在设计时考虑减重优化,降低理论用量;二是提升材料利用率,减少材料耗费。当然,选用主流产品的材料体系,也可降低材料采购单价,从而达到降低材料成本的目的。
在制造过程中,一般从以下几方面着手,考虑提高材料利用率:料层边界优化及拼搭接工艺方案优化;料片排版优化;减少工艺余量,优化自动铺带程序、下料程序;调整胶膜的下料方式;大批量生产阶段,实现同类材料的混排下料。
提升铺贴效率,降低工时成本
在降低材料成本之外,提升铺贴效率,降低工时成本也是降低复合材料成本的常用方法之一。目前民机复合材料的铺贴大多采用手工铺贴、自动铺带(ATP)和自动丝束铺放(AFP)等。
手工铺贴由于不用设备,工时成本仅有人工成本,但其依赖于铺层工人的素质,废品率高,且效率低,近年仅在小零件上应用。20世纪60年代,在美国空军航空材料实验室的资助下,美国的制造商就开展了自动铺带研究,并在20世纪80年代正式用于航空制造。自动铺带的主要优点是适合于大型结构,特别是平面结构,能做到省工省时。自动丝束铺放技术是纤维缠绕与自动铺带的结合,铺放效率高,材料浪费少。现阶段国内自动铺带综合效率不高,迫切需要提升铺带效率,降低铺贴成本。
综合来看,提升自动铺带的效率,可以从几个方面着手:在铺层设计上,尽可能减少铺层递减;在工序优化上,要明确铺带机区域内外工作,明确材料待加工区,在材料优化上,要上调原材料覆卷张紧力,有效改善铺层褶皱问题;在智能检测上,可引入5G视觉检测,搭建拼缝和多余物检测系统,提高检测的效率和准确性;在标准化上,要形成编程指南,实现标准化编程、现场标准化流程操作。
优化拼罐固化方案,降低工时成本
热压罐成型工艺是目前的主流固化工艺,短期内无法用液体成型工艺等来替代,因此,改进热压罐成型工艺对于降低复合材料的制造成本也具有非常重要的意义。
热压罐是一个具有整体加热加压功能的大型压力容器,由于其耗能、使用和维护成本高,在复合材料制造成本中占有相当大的比重,如何提高热压罐设备的利用率是降低成本的关键。
在目前的复合材料生产过程中,为提升热压罐成型的效率,一般会同时固化多个零件。该工艺生产中确实能大大提升固化效率,但在实际操作中,为了保证所有零件的质量,需要充分考虑设备的固化能力、零件工装形式、零件在热压罐中的排布等各种因素。如果零件在热压罐中排布不合理,会造成热压罐中热空气循环不畅通,甚至有循环死角,从而使罐内温度不均匀,影响到零件的固化质量。
为了防止这种情况的发生,在零件固化前,需要先根据零件的固化参数、工装形式和设备能力等对所有的零件进行分组,并对同一组零件在热压罐中的摆放位置、摆放方向进行模拟,以确定不同组合方式下热压罐内部的温度分布,优化出最佳的产品组合方式。工艺模拟和优化后,还需要对同一组零件进行实际的热分布测试,即将所有的工装按照模拟的位置和方向放入热压罐中,并在所有工装上按照一定的要求均匀布置热电偶,按照实际的固化参数进行模拟固化,以确定同一组零件固化时罐内实际的温度最高点和最低点,升降温速率、加压点等工艺参数。
当然,在拼罐固化的过程中,必须高要求严格实施,否则将造成批量零件的损失。因此,拼罐固化在体现热压罐高效率使用的同时,也给如何保证零件的质量带来了挑战。
工装优化,降低工装成本
工装包含制造过程中的成型工装和检测工装等,可重复使用,在工装成本的控制上,通常从工装材料选择、工装设计和统筹管理等方面进行优化。
在工装材料选择方面,减少高成本材料用量,在大型工装中采用殷瓦钢面板加普通钢框架的形式,减少非成型面的殷瓦钢使用量,同时编制工装设计规范,明确工装选材原则。在工装设计方面,在满足制造要求的情况下,尽可能采用简单形式工装,设计阶段并行设计,工装与工程设计、零件工艺同步,缩短工装采购周期。在工装统筹管理方面,建立工装需求表,制定工装年度计划,识别工装可替代性,评估工装的必要性;建立工装数据库,统筹调用各型号、各项目所需工装。
复合材料的制造成本和设计、制造一体化是一个既系统复杂又需权衡利弊的过程。设计要全方位考虑成本控制,将成本意识贯穿于设计、工艺、采购、制造的全过程。开展复合材料面向成本的设计和制造技术研究,提高复合材料制造过程中的材料利用和资源使用,是降低复合材料制造成本的根本。结合民机经济性需求,加大力度开展复合材料成本分析控制以及低成本技术研究,对促进我国民机行业发展具有重要意义。
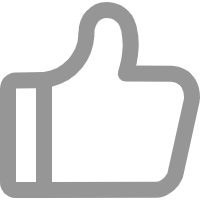
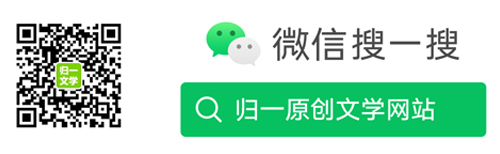