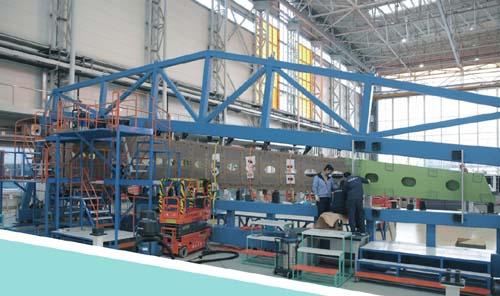
数十年来,随着市场对飞机性能要求的不断提高,飞机上的结构和系统逐渐增多,飞机也变得越来越“臃肿”。与人类似,飞机超重也会引起一系列的问题。为此,设计师们日益关注飞机的“体重”,轻量化设计便是助力飞机“瘦身”的一种有效途径。
轻量化的优势
轻量化这一概念起源于赛车运动,如今已广泛应用到汽车、建筑、航空航天等领域。飞机轻量化的优势不难理解,单从经济角度来看,以可搭载400余人的波音747-400为例,其最大燃油容量为216840升,满载航程1.3万公里,大概为美国洛杉矶到上海的距离,单程燃油成本超过10万美元。
由于飞机的油耗巨大,轻量化所带来的燃油成本减少不容小觑。因此,我们不难理解为什么波音在787飞机研制过程中,愿意投入3亿美元来研究飞机某个部位以钛合金替代铝合金的可行性,以此达到减重2500千克的目标。
另外,飞机轻量化设计也与绿色航空的理念相契合。全球气候变暖以及环境污染的加剧,使得减少航空碳排放迫在眉睫。国际民航组织计划到2050年商用飞机的碳排放减少一半。为了实现这一目标,一方面要使用清洁能源,另一方面也要通过轻量化设计等方法来提高燃油效率。从技术角度来讲,轻量化有助于提升飞机的性能,如飞行速度、载重量、推重比和升力等。
对于商用飞机来说,更大的推重比意味着更大的运力。波音737-900系列飞机的载客量为203人,已经是第一代737-100系列飞机的一倍以上。轻量化设计在增加飞机运客量的同时,也给乘客带来了更宽敞的空间、更完善的空中设施以及更快捷的飞行体验。
三种主要途径
大体而言,飞机轻量化技术可以分为轻量化材料应用、结构优化设计和先进制造工艺三种主要途径。其中,常见的轻量化材料包括铝合金、钛合金、高强度钢和复合材料等,结构优化设计包括尺寸优化、形状优化和拓扑优化,先进制造工艺包括增材制造、先進金属制造工艺等。
新型材料
在飞机的结构设计中,材料选择是关键一环,“一代材料,一代飞机”的说法更是把材料对于飞机的重要性表现得淋漓尽致。自1903年美国莱特兄弟用木材、钢材和布制造出第一架飞机以来,飞机材料的发展经历了五个阶段。目前,商用飞机使用的材料主要有复合材料、铝、钛、钢等。
以碳纤维增强聚合物(CFRP)为主的复合材料,具有可设计性好、密度低、高强度、高模量、抗疲劳性好、耐腐蚀等优点。与普通钢材相比,其重量减轻了75%,而强度却提高了4倍。复合材料最开始被应用于军用飞机,用量由少到多,部位由一般结构到主承力结构,经过几十年的经验积累后,才逐步应用到商用飞机上。
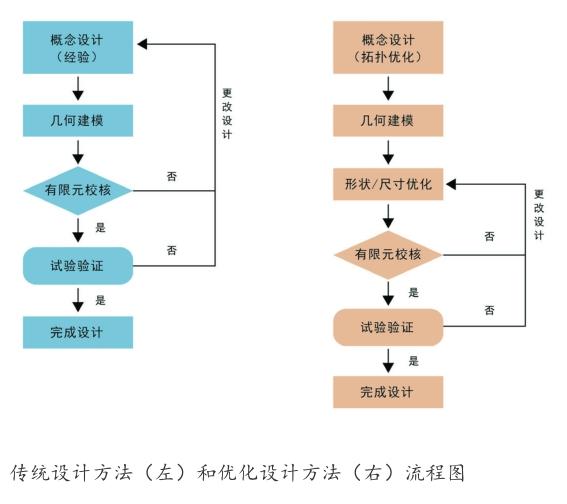
如今,复合材料的用量、应用部位及工艺水平已经成为衡量大型飞机先进程度的一个重要指标,波音787和空客A350XWB的复合材料用量都占50%以上。复合材料不仅可以减轻飞机的重量,而且还改善了飞机的耐腐蚀性和抗疲劳性能,降低了维护费用,大幅度提高了飞机的经济性和环保性。
尽管复合材料已成为未来航空材料的主流,但从目前来看,其成本还是过高,因此,经过长期考验的、不断改进的传统金属材料还是首选。在传统金属材料中,铝、钛、钢等材料仍占主导地位。铝合金质轻、耐腐蚀、比强度高,是应用最广的有色金属结构材料,很多飞机型号的机身蒙皮、外翼蒙皮、机翼长桁等都采用铝合金。由于热处理技术的发展,新品种的铝合金不断出现,特别是第三代铝锂合金,不仅具有低密度、高弹性模量、高比强度和高比模量等优点,同时还兼具低疲劳裂纹扩展速率、较好的高温低温性能,被认为是最理想的航空航天材料之一。中国商飞C919飞机大量使用了第三代铝锂合金,减重效果十分明显。
钛合金作为近几十年发展的新型轻金属材料,具有高强高模、高损伤容限、耐高温、耐腐蚀性等优点。然而,较差的可制造性和高成本(通常是铝合金成本的8倍以上)限制了钛合金在飞机结构上的大量使用。目前,钛合金主要用在有高强度、抗腐蚀需求但空间有限的区域,如飞机机体结构和航空发动机部件。

优化设计
在传统的设计过程中,设计师会依靠自身经验或参考现有机型的结构,先初步设定每个零件的尺寸大小和位置分布,再通过模拟试验收集数据,计算校核设计方案的可行性,这种方法往往需要进行多次反复才能达到设计要求。总体而言,传统的设计过程往往更注重结构的强度和寿命等安全性因素,减重效果并不理想。
在使用优化设计方法时,设计师首先会根据设计的空间、约束以及目标,建立初步有限元模型,通过优化计算,得出初步的最优拓扑关系(即材料分布),然后在这一基础上建立几何模型,再经过尺寸和形状优化,进一步优化参数,最终通过有限元校核和试验进行验证,从而得到最优的设计结果。
结构优化设计在航空领域中主要采用三种方法:尺寸优化、形状优化和拓扑优化。
尺寸优化是确定结构最佳尺寸的最基本方法,主要对象是杆件截面积、板壳厚度等。形状优化主要针对结构外边界或孔洞形状,但最终结构的连通性不会改变。拓扑优化用于确定设计域内最佳材料分布,从而使结构能在满足特定约束条件下,将外载荷传递到结构支撑位置,同时结构的某种形态指标达到最优,在实现结构减重的同时,也增强了结构的性能。
先进制造工艺
可制造性是飞机结构设计过程中的一个关键要素,它决定了设计方案是否能制造成真实的产品。因此,在材料选择、结构优化设计过程中,设计师必须考虑可制造性方面的问题。例如,钛合金具有非常高的比强度和其他优良性能,但它们的应用受到高制造成本的限制,拓扑优化设计的结果往往是复杂的几何形状,有时不能通过铸造等传统制造工艺制造。
以增材制造为代表的新型制造工艺是飞机结构轻量化的关键。相对于传统对原材料去除、切削、组装的加工模式,增材制造是一种“自上而下”材料累积的制造方法,可以制造出具有复杂几何形状的结构,并且可以释放制造约束,增强结构设计的灵活性。设计灵活性的提升使结构的整体化制造成为可能,而零件数量的减少往往意味着整体结构变得更轻。
以复合材料结构制造为例,常见的复合材料制造工艺一般是先铺放预成型,然后放入热压罐固化成型。由于零件结构复杂,需要配套复杂的模具工装,一方面模具成本高,另一方面制件铺放预成型的难度大、工时长,无形中增加了制造成本。而复合材料增材制造不需要工装,也没有后续的热压罐固化,节约了热压罐设备采购和运行成本、固化过程中的辅助材料以及工艺运转成本。因此,从长期发展来看,增材制造技术的应用前景十分看好。
未来发展趋势
随着技术水平的不斷提高,飞机轻量化在材料、结构优化设计、先进制造工艺等方面呈现出越来越快的发展趋势。
在轻量化材料方面,首先,飞机的更新换代对其使用材料的性能提出了更高的要求;其次,对传统材料的持续改进仍在进行;第三,更加强调飞机结构材料的技术转移和产业化。目前,复合材料向耐高温、智能化方向发展,碳纤维、陶瓷基复合材料和树脂基复合材料是发展重点。金属结构则向着轻量化、复合化方向发展,轻质耐高温金属和金属纳米复合材料是发展重点。
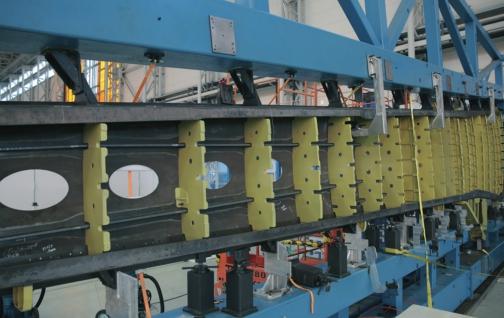
飞机结构优化设计朝着数字化方向发展,OptiStruct、MSC Nastran等计算机辅助软件的应用越来越广泛。提高结构效率、减轻结构重量是优化设计的目标,数字化算法是提升优化设计效率的关键,大型整体承力结构和功能一体化结构是现阶段优化设计应用的重点对象。
先进制造工艺水平也有望在近几年得到大幅提高。对于复合材料结构,整体化和精密自动化是发展方向。大型制造工艺设备和非热压罐低温固化技术发展迅猛,有利于复合材料结构整体化制造。高精度自动化成型技术,如自动铺带、自动铺丝、挤压成型等,在飞机主承力结构制造上的运用越来越广泛。
对于金属材料结构,整体加工、数控加工和新型制造技术是发展方向。大型壁板采用喷丸成形、压弯成形等技术实现整体制造。未来,飞机上仍会有大量数控加工件,数控加工将向更加精密、高效的方向发展。泡沫金属成型、热成型淬火、超塑性成型等制造工艺的发展,为制造复杂结构件提供了保障。与此同时,无论是复合材料结构,还是金属结构,增材制造技术都具有巨大的潜力,这将是未来飞机结构制造工艺的一个重要发展方向。
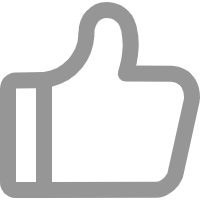
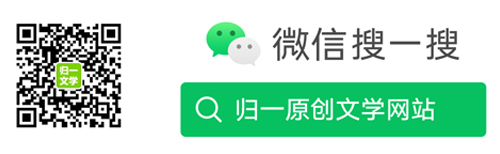