1 引言
近年来,随着机动车愈来愈大众化【1】,机动车生成厂商进一步加大了生产力度。国家相关政策要求【2】【3】【4】【5】,在机动车出厂之前需要对其电子器件特性进行测试,只有检测合格的机动车才能进入市场。待检机动车数量的增加与检测车间缓慢的检测效率之间的矛盾越来越尖锐。因此,提升检测设备利用率、优化检测车间检测效率、提升机动车检测效率刻不容缓。本文从检测车间布局出发,将当前的顺序布局改进为并行布局,从硬件层面提升机动车检测效率。当前工业使用的机动车检测策略是顺序布局结合先来先服务(First In First Out, FIFO)策略的检测模式【6】【7】。陈昌领等【8】对汽车综合性能检测线批次检测车辆的建模与短期调度问题的研究,提出了一些关于汽车综合性能检测线批次车辆检测排序和驾驶员人数安排的指导建议。黄文兵【9】通过研究汽车综合性能检测站的车间布局设计,基于批处理过程对给定数量的车辆上线检测短期调度进行建模,实现了汽车检测车间布局的优化。
本文结合并行策略,将检测车间并行化优化,提出了一种基于并行策略的机动车检测站工位布局优化模型。本文主要贡献为:
⑴ 优化检测车间布局,改顺序布局为并行布局,使得各检测设备可以并行检测机动车,从硬件层面提升机动车的检测效率。
⑵ 提升检测设备的利用率。减低了检测设备空转时间。
本文后续部分的组织如下:第2节介绍了并行车间的设计思路;第3节给出了算法仿真过程以及对仿真结果进行了对比分析;最后是结论和对未来研究方向的展望。
2 并行车间设计
当前检测车间布局为顺序布局,各检测工位顺序排列。机动车在完成上一个检测任务后,才能进入下一个检测工位。这样存在一个明显的问题:当机动车在上一个工位完成检测任务时,如果当前工位有机动车在检测,那么只能在上一个工位等待。这样必然导致完成检测任务的机动车持续占用检测工位,使得在该工位有检测任务的机动车不能及时进入检测。检测车间顺序布局,如图1所示。
图1 顺序布局
当检测车间为顺序布局时,机动车按照箭头方向,依次完成各工位的检测任务。当下一个工位有车辆时,在本工位等待。为了解决机动车完成检测任务仍在工位等待的问题,提出检测车间并行布局,如图2所示。

图2 并行布局
当检测车间为并行布局时,机动车按照箭头方向,依次完成各工位的检测任务。即当机动车完成检测任务时,立即驶离检测工位,检测工位等待下一辆机动车检测。并行布局可以完美的解决顺序布局带来的机动车完成检测任务仍在该工位等待的问题。
3 验证实验
3.1 性能评价标准
⑴调度时间完成一批机动车的检测任务时,最后一辆机动车的完成检测时间。
⑵总等待时间
机动车完成检测项目申请到完成所有检测任务之间的等待时间称为该机动车等待时间。总等待时间表示为所有机动车的等待时间之和。机动车等待时间也可转换为:机动车结束检测时刻、开始检测时刻、检测任务总耗时,三者之差。平均等待时间,指总等待时间与检测机动车总数之间的比值。
⑶资源利用率
完成一批机动车的检测任务后,检测工位检测机动车的时间与检测工位总运行之间的比值。
3.2 实例分析
将机动车的检测项目和各项目的检测耗时进行抽象,如表1所示。
表1 工位和检测项目对应关系(分钟)
5辆机动车{A, B, C, D, E}, 均申请表1中的检测项目。分别将该5辆机动车在顺序布局和并行布局上进行调度,机动车的调度过程,如图3和图4所示。

图3 并行布局检测Gantt图

图4 顺序布局检测Gantt图
结合图4可知,采用顺序布局,5辆机动车在3个检测工位上的调度耗时为39,机动车总等待时间为60,资源利用率为72.82%;结合图4可知,采用并行布局,5辆机动车在3个检测工位上的调度耗时为30,机动车总等待时间为33,资源利用率为100%;。通过实例对比,本文提出的并行布局在完成相同检测任务的前提下,具有总调度时间短、等待时间短、资源利用率高的特点。
4 结论
本文提出了一种基于并行策略的机动车检测站工位布局优化模型。该模型将顺序检测车间优化为并行检测车间。通过实例分析可知,相比于顺序布局,待检机动车的平均调度时间减少23.07%、平均等待时间减少45%;检测机构的资源利用率提高27.18%。本文提出的检测车间并行布局模型,在硬件层面提升了检测车间的检测效率。在下一步准备结合实际情况,对机动车检测调度算法进行研究。
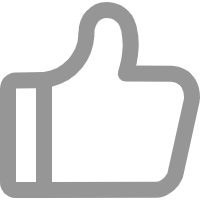
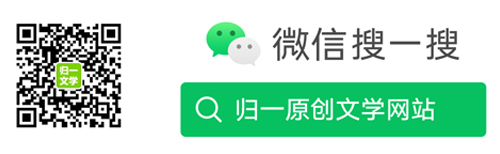